Kaizen
(改善, “cambio para mejorar” o “mejoramiento” en japonés; el uso común de su traducción al castellano es “mejora continua” o “mejoramiento continuo”).
En su contexto este artículo trata de Kaizen como una estrategia o metodología de calidad en la empresa y en el trabajo, tanto individual como colectivo. Kaizen es hoy una palabra muy relevante en varios idiomas, ya que se trata de la filosofía asociada al sistema de producción Toyota, empresa fabricante de vehículos de origen japonés.“¡Hoy mejor que ayer, mañana mejor que hoy!” es la base de la milenaria filosofía Kaizen, y su significado es que siempre es posible hacer mejor las cosas. En la cultura japonesa está implantado el concepto de que ningún día debe pasar sin una cierta mejora. Durante los años 50 del siglo pasado, en Japón, la ocupación de las fuerzas militares estadounidenses trajo consigo expertos en métodos estadísticos de Control de calidad de procesos que estaban familiarizados con los programas de entrenamiento denominados TWI (Training Within Industry) cuyo propósito era proveer servicios de consultoría a las industrias relacionadas con la Guerra.
Los programas TWI durante la posguerra se convirtieron en instrucción a la industria civil japonesa, en lo referente a métodos de trabajo (control estadístico de procesos). Estos conocimientos metodológicos los impartieron W. Edwards Deming y Joseph M. Juran; y fueron muy fácilmente asimilados por los japoneses. Es así como se encontraron la inteligencia emocional de los orientales (la milenaria filosofía de superación), y la inteligencia racional de los occidentales y dieron lugar a lo que ahora se conoce como la estrategia de mejora de la calidad Kaizen. La aplicación de esta estrategia a su industria llevó al país a estar entre las principales economías del mundo. Este concepto filosófico, elemento del acervo cultural del Japón, se lo lleva a la práctica y no sólo tiene por objeto que tanto la compañía como las personas que trabajan en ella se encuentren bien hoy, sino que la empresa es impulsada con herramientas organizativas para buscar siempre mejores resultados.
Partiendo del principio de que el tiempo es el mejor indicador aislado de competitividad, actúa en grado óptimo al reconocer y eliminar desperdicios en la empresa, sea en procesos productivos ya existentes o en fase de proyecto, de productos nuevos, del mantenimiento de máquinas o incluso de procedimientos administrativos. Su metodología trae consigo resultados concretos, tanto cualitativos como cuantitativos, en un lapso relativamente corto y a un bajo costo (por lo tanto, aumenta el beneficio) apoyado en la sinergiaque genera el trabajo en equipo de la estructura formada para alcanzar las metas establecidas por la dirección de la compañía. Fue Kaoru Ishikawa el que retomo este concepto para definir como la mejora continua o Kaizen , se puede aplicar a los procesos , siempre y cuando se conozcan todas las variables del proceso .
Etimología: Los caracteres originales para esta palabra son 改善 (pronunciado kaizen en japonés; gǎishàn en chino), donde:
- 改 (かい)(kai en japonés, gǎi en chino) significa ‘cambio’ o ‘la acción de enmendar’.
- 善 (せん)(zen en japonés, shàn en chino) significa ‘bueno’ o ‘beneficioso’.
‘Beneficioso’ está más relacionado con el Taoísmo o con la filosofía budista, que da la definición de un beneficio común, de la sociedad y no de intereses individuales (p.e. mejora multilateral). En otras palabras, una persona no se puede beneficiar a expensas de otra. El beneficio que concierne a este concepto debe ser sustentable (para siempre), Zen o Shan es un término que refleja un acto realmente altruista, que beneficie a otros.
Las 5S
El método de las 5S, así denominado por la primera letra del nombre que en japonés designa cada una de sus cinco etapas, es una técnica de gestión japonesa basada en cinco principios simples. Se inició en Toyota en los años 1960 con el objetivo de lograr lugares de trabajo mejor organizados, más ordenados y más limpios de forma permanente para conseguir una mayor productividad y un mejor entorno laboral. Las 5Shan tenido una amplia difusión y son numerosas las organizaciones de diversa índole que lo utilizan,tales como, empresas industriales, empresas de servicios, hospitales, centros educativos o asociaciones.
La estrategia de las 5S es un concepto sencillo que a menudo las personas no le dan la suficiente importancia, sin embargo, una fábrica limpia y segura nos permite orientar la empresa y los talleres de trabajo hacia las siguientes metas:
· Dar respuesta a la necesidad de mejorar el ambiente de trabajo, eliminación de despilfarros producidos por el desorden, falta de aseo, fugas, contaminación, etc.
· Buscar la reducción de pérdidas por la calidad, tiempo de respuesta y costes con la intervención del personal en el cuidado del sitio de trabajo e incremento de la moral por el trabajo.
· Facilitar crear las condiciones para aumentar la vida útil de los equipos, gracias a la inspección permanente por parte de la persona quien opera la maquinaria.
· Mejorar la estandarización y la disciplina en el cumplimiento de los estándares al tener el personal la posibilidad de participar en la elaboración de procedimientos de limpieza, lubricación y apriete
· Hacer uso de elementos de control visual como tarjetas y tableros para mantener ordenados todos los elementos y herramientas que intervienen en el proceso productivo
· Conservar del sitio de trabajo mediante controles periódicos sobre las acciones de mantenimiento de las mejoras alcanzadas con la aplicación de las 5S
· Poder implantar cualquier tipo de programa de mejora continua de producción Justo a Tiempo, Control Total de Calidad y Mantenimiento Productivo Total
· Reducir las causas potenciales de accidentes y se aumenta la conciencia de cuidado y conservación de los equipos y demás recursos de la compañía.
· Buscar la reducción de pérdidas por la calidad, tiempo de respuesta y costes con la intervención del personal en el cuidado del sitio de trabajo e incremento de la moral por el trabajo.
· Facilitar crear las condiciones para aumentar la vida útil de los equipos, gracias a la inspección permanente por parte de la persona quien opera la maquinaria.
· Mejorar la estandarización y la disciplina en el cumplimiento de los estándares al tener el personal la posibilidad de participar en la elaboración de procedimientos de limpieza, lubricación y apriete
· Hacer uso de elementos de control visual como tarjetas y tableros para mantener ordenados todos los elementos y herramientas que intervienen en el proceso productivo
· Conservar del sitio de trabajo mediante controles periódicos sobre las acciones de mantenimiento de las mejoras alcanzadas con la aplicación de las 5S
· Poder implantar cualquier tipo de programa de mejora continua de producción Justo a Tiempo, Control Total de Calidad y Mantenimiento Productivo Total
· Reducir las causas potenciales de accidentes y se aumenta la conciencia de cuidado y conservación de los equipos y demás recursos de la compañía.
La integración de las 5S satisface múltiples objetivos. Cada ‘S’ tiene un objetivo particular:
- Mejorar las condiciones de trabajo y la moral del personal. Es más agradable y seguro trabajar en un sitio limpio y ordenado.
- Reducir gastos de tiempo y energía.
- Reducir riesgos de accidentes o sanitarios.
- Mejorar la calidad de la producción.
- Seguridad en el trabajo.
Aunque son conceptualmente sencillas y no requieren que se imparta una formación compleja a toda la plantilla, ni expertos que posean conocimientos sofisticados, es fundamental implantarlas mediante una metodología rigurosa y disciplinada.
Se basan en gestionar de forma sistemática los elementos de un área de trabajo de acuerdo a cinco fases, conceptualmente muy sencillas, pero que requieren esfuerzo y perseverancia para mantenerlas.
Las 5S, se implementan de forma paulatina y solo una a la vez, luego de haber implementado con exito una de ellas se continua con la siguiente hasta alcanzarlas a todas.
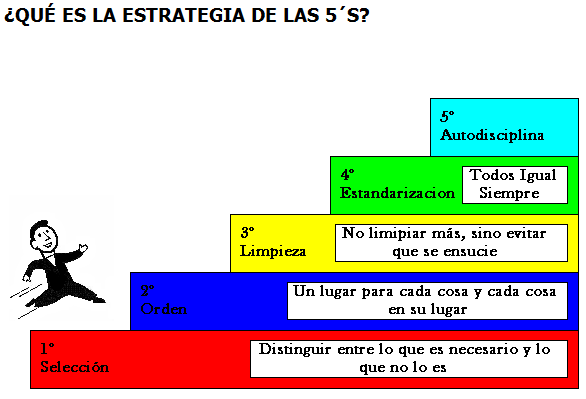
La implementación de cada una de las 5S se lleva a cabo siguiendo cuatro pasos:
- Preparación: formación respecto a la metodología y planificación de actividades.
- Acción: búsqueda e identificación, según la etapa, de elementos innecesarios, desordenados (necesidades de identificación y ubicación), suciedad, etc.
- Análisis y decisión en equipo de las propuestas de mejora que a continuación se ejecutan.
- Documentación de conclusiones establecidas en los pasos anteriores.
El resultado se mide tanto en productividad como en satisfacción del personal respecto a los esfuerzos que han realizado para mejorar las condiciones de trabajo. La aplicación de esta técnica tiene un impacto a largo plazo. Para avanzar en la implementación de cualquiera de las otras herramientas de Lean Manufacturing es necesario que en la organización exista una alto grado de disciplina. La implementación de las 5S puede ser uno de los primeros pasos del cambio hacia mejora continua.
El principio de las 5′s puede ser utilizado para romper con los viejos procedimientos existentes e implantar una cultura nueva a efectos de incluir el mantenimiento del orden, la limpieza e higiene y la seguridad como un factor esencial dentro del proceso productivo, de calidad y de los objetivos generales de la organización.
Es por esto que es de suma importancia la aplicación de la estrategia de las 5 S´s, no se trata de una moda sino de un nuevo modelo de dirección o un proceso de implantación que mejora nuestra organización.
No hay comentarios:
Publicar un comentario